As we all know, with the rapid development of modern industrial technology, in order to improve production efficiency, improve product quality, and reduce production costs, the requirements for temperature control in the production process are getting higher and higher.
However, there are more and more failure problems of some chillers, so we have conducted a brief analysis of some failure problems of chillers
First, the failure analysis of the chiller:
1. Abnormal temperature of cooling water inlet and outlet: the inlet water temperature of the condenser is too high (higher than 32), first check whether the fan of the cooling tower is reversed (there is such an example in the actual project); Under the premise, adjust the angle of the fan blades to increase the air volume of the fan
There is also a phenomenon that often occurs in a system where multiple cooling towers are used in parallel. When part of the load is running, the temperature difference between the inlet and outlet of the condenser is small. It is necessary to check whether each cooling tower has an electric valve, or whether the electric valve has been set. Failure to cause cooling water bypass, incomplete cooling
2. The pressure difference between the inlet and outlet of the cooling water is constant; according to the relevant refrigeration theory, the heat release of the condenser directly affects the cooling capacity. Therefore, the cooling water system should be checked first.
Based on the pressure loss value on the nameplate of the main engine, if the pressure difference value from the reading of the pressure gauge at the inlet and outlet greatly exceeds the normal value, it means that the inlet of the condenser is blocked by debris
Open the water seal head at the inlet end, it can be seen that the diameter of the copper pipe is small. Since the cooling water is an open system, the sundries are scattered in the water collecting tray and enter the system with the water flow. Once the water filter mesh is broken down, it will be collected to the inlet of the condenser place, so remove debris
2. Maintenance and maintenance of the chiller: the use of the chiller can reduce the preheating time of the mold, improve the surface quality of the finished product and enable fully automated production
Improving mold life is a necessary means to increase productivity
The use of chillers in other industries is a necessary condition for equipment composition, and the names are different.
It is called oil heater in roller temperature control of PVC sheet, temperature control device in extruder equipment, and temperature control system or temperature control machine in rubber mixer equipment. Rapid heating, followed by the process of keeping warm
Industrial chiller (chiller) ice water machine maintenance: keep the surface of the industrial chiller (chiller) ice water machine clean, clean the ice water and cooling filter regularly, the industrial chiller (chiller) ice water machine has been used for more than six month, or the high and low pressure engines often fail, or the cooling capacity is reduced, please check whether the pressure of the high pressure gauge is higher than 300PSI
If it exceeds, the staff should be arranged to clean the condensation, keep it clean, and improve the effect of the radiator
1 . Screw compressor Screw compressor is a very critical component in the unit, the quality of the compressor is directly related to the stability of the unit
If the compressor fails. Due to the high installation accuracy requirements of screw compressors, it is generally necessary to ask the factory for maintenance.
2 . Cleaning of the condenser and evaporator The cooling water of the water-cooled condenser is an open circulation loop, and the tap water generally used is circulated through the cooling tower.
When the content of calcium salt and magnesium salt in the water is large, it is easy to decompose and deposit on the cooling water pipe to form scale, which affects the heat transfer.
If the scale is too thick, the cooling water circulation section will be reduced, the water volume will be reduced, and the condensing pressure will rise.
Therefore, when the quality of the cooling water used is poor, the cooling water pipes should be cleaned at least once a year to remove scale and other dirt in the pipes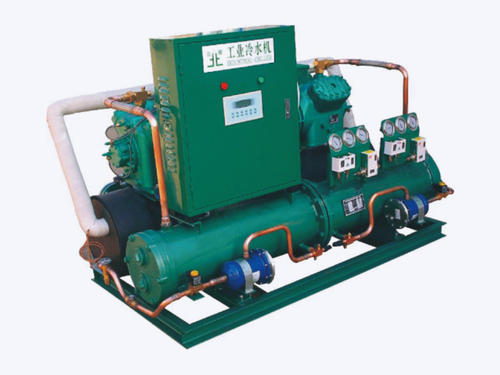
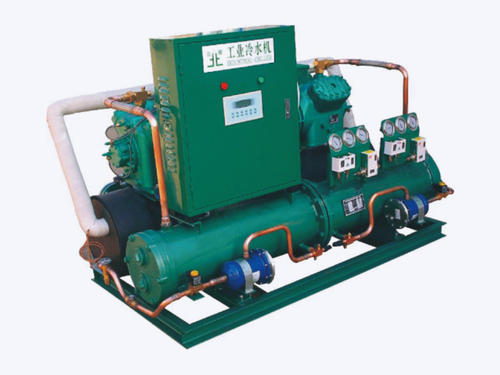